Staveb Automation AG utilizează controlere OMRON (PLC) pentru retehnologizare. Compania de produse alimentare elveţiană Delica AG înlocuieşte sistemele de comandă şi tehnologia de acţionare pentru productivitate sporită, reducerea pierderilor şi ambalare mai rapidă.
Utilajele din producţia de alimente şi băuturi trebuie să fie fiabile, sigure, rapide şi să păstreze calitatea timp de mai mulţi ani sau chiar decenii. Sunt necesare tehnologii de înaltă performanţă şi întreţinere continuă, iar utilajele trebuie să satisfacă şi cele mai recente standarde, specificaţii şi cerinţe ale companiei. Aşa-numitele soluţii de retehnologizare, respectiv modernizarea sau extinderea fabricilor şi echipamentelor existente sunt esenţiale în privinţa competitivităţii şi valorii viitoare. Staveb Automation AG, cu sediul în Hitzkrich, cantonul elveţian Lucerna, este specializată în aceste soluţii de retehnologizare, pe lângă automatizarea industrială, robotică şi tehnologiile de comandă. De astfel de actualizări se bucură, în special, fabricile de producţie semiautomate şi complet automate, care funcţionează cu sisteme de comandă depăşite, dar acestea trebuie adaptate cu precizie la cerinţele companiei respective. Ca partener vechi de soluţii , Staveb foloseşte tehnologiile de comandă ale expertului internaţional în automatizare, OMRON. Exemplul companiei alimentare elveţiene Delica AG demonstrează avantajele unui astfel de proiect de retehnologizare în domeniul producţiei de cornete pentru îngheţată.
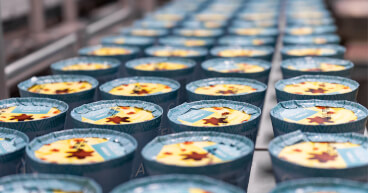
Lipsa pieselor de schimb şi echipamentele depăşite afectează productivitatea
Dacă fabricile şi liniile de producţie trebuie modernizate, companiile urmăresc să obţină în primul rând eficienţă. Pe de altă parte, sunt obligate să găsească noi soluţii, deoarece asistenţa devine incertă, piesele de schimb lipsesc sau actualizările sistemelor nu mai sunt disponibile. Problema: reparaţiile necesită stocuri, echipamentele nu sunt disponibile tot timpul, iar producţia se blochează. Staveb a ajutat companii dintr-o gamă largă de domenii în modernizarea fabricilor şi proceselor de aproximativ trei decenii. În acest timp, tehnologiile s-au schimbat extrem de mult, procesele au devenit din ce în ce mai automatizate şi soluţiile din ce în ce mai conectate. Ce nu s-a schimbat: îngheţata la vafă, sau la cornet este la fel de îndrăgită azi, ca acum 30 de ani. Dacă în timpul producţiei lipseşte o piesă de schimb, acest lucru poate cauza pierderi serioase în producţie, ceea ce companiile ca Delica, fosta Midor, vrea să evite cu orice preţ.
Identificarea şi eliminarea mai rapidă a defecţiunilor
Din aceste motive fabricile trebuie să rămână mereu actualizate. Sistemele moderne de comandă sunt cheia, deoarece ajută la diagnosticarea mai rapidă şi mai uşoară a defecţiunilor. Mai mult, acest tip de modernizare creşte productivitatea. Acest lucru poate fi obţinut, de exemplu, prin achiziţii de date şi comunicare mai rapide, asigurându-se astfel o flexibilitate mai mare în timpul modificărilor de produse. Delica AG din Meilen a ales modernizarea pentru că sistemul de comandă utilizat în prealabil nu mai este produs şi nu mai beneficiau de asistenţă. Totodată, software-ul de programare al sistemului, realizat în anii 90, nu mai rula în mediul actual Windows. „Sistemul funcţiona bine, dar pe lângă problema de comandă, uzura era prea mare şi piesele de schimb deveneau din ce în ce mai scumpe. Astfel, am integrat noi axe servo şi am înlocuit angrenajele susceptibile,” a spus Urs Weber, şef de echipă pentru automatizare/electrică IH la Delica.
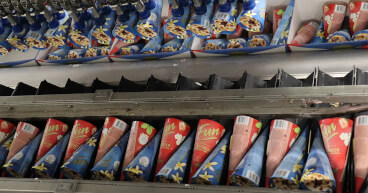
Accentul pus pe oameni
„A mai existat şi un număr din ce în ce mai mare de defecţiuni în tehnologia de angrenare, iar piesele de schimb mecanice uneori aveau termen de livrare de mai multe luni, precum şi preţuri astronomice, un fapt nedorit, desigur. Totodată, securitatea utilajului nu mai era de ultimă oră,” a adăugat Michael Engler, COO al Staveb Automation AG. Pe lângă sistemele de comandă, oferta de retehnologizare Staveb a inclus tehnologia de acţionare, angrenare şi comandă, tehnologia de securitate şi senzori, precum şi sisteme de măsurare, dacă era cazul. Accentul tuturor proiectelor a fost pus pe operatori şi pe cei responsabili cu întreţinerea, a căror muncă trebuie simplificată. Soluţiile de interfaţare om-maşină (HMI) simplifică şi mai mult manipularea maşinilor. Pe lângă producţia de îngheţată, Staveb a modernizat şi linii de umplere cu varză murată, pasteurizarea pastelor proaspete, ambalarea chiftelelor hamburger, a legumelor sau a salatelor destinate consumului imediat.
Soluţie dintr-o singură sursă şi asistenţă personalizată
Delica nu era străină de companiile Staveb şi OMRON, dar a folosit în trecut soluţii de la alţi furnizori în privinţa tehnologiilor de angrenare. În cadrul proiectului de modernizare, totul trebuia unificat. „Utilizatorii echipamentelor trebuie să aibă mereu aceeaşi interfaţă GUI în faţa lor,”, spune Engler. Staveb a folosit unităţile de comandă OMRON la diverse proiecte de retehnologizare încă din anul 2003. Clienţii se bucură nu doar de mulţi ani de experienţă nu doar din partea experţilor în automatizare, dar şi de faptul că primesc o soluţie personalizată dintr-o singură sursă şi fără eforturi majore privind implementarea. „Colaborăm cu OMRON pentru că sunt foarte apropiaţi de client - inginerii de aplicaţii, în special, răspund imediat solicitărilor dacă apare vreo întrebare,” explică Engler.
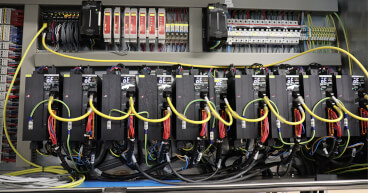
Baza este formată de o platformă de automatizare Sysmac, alături de angrenajele 1S de la OMRON, cu integrare continuă de la controlerul de utilaj bazat pe NX/NJ până la software. Cu ajutorul platformei software Sysmac, funcţionalitatea PLC, controlul mişcării, controlul roboţilor, HMI, securitatea şi sistemele de camere pot fi complet integrate şi incluse într-o reţea. Sysmac a fost folosit în sistemele PLC începând cu 1971. „Sysmac este mai deschis faţă de soluţiile altor furnizori, uşurând astfel extrem de mult adaptarea producţiei,” spune Reto Stenico, manager regional de vânzări pentru Elveţia la OMRON. Acesta spune că platforma permite utilizatorilor să reacţioneze mai flexibil la modificări, să controleze intrările eronate şi să se adapteze mai rapid la noile cerinţe din piaţă: „Simplifică configurarea liniei de producţie.”
Mai puţine pierderi, ambalare mai rapidă
O altă provocare a proiectului Delica a fost multitudinea de modificări din producţie: pe lângă gama bogată de arome, existau aproximativ 30 de toppinguri pentru îngheţată şi 20 de forme care trebuiau luate în considerare la fiecare modificare de producţie. În trecut, se întâmpla ca aproximativ 30.000 de îngheţate la vafă să nu poată fi comercializate în timpul schimbărilor. Datorită fabricii mai moderne, modificările de producţie acum sunt realizate fără rebuturi. Mai mult, procesul de ambalare acum este mai rapid cu 10 - 20 procente.
Proiect de retehnologizare cu impact imens
IoT, inteligenţa artificială (AI), sau învăţarea automată (ML) sunt adesea subiecte de discuţii în contextul Industrializării 4.0. Dar, uneori, nu inovaţiile majore raţionalizează şi impulsionează producţia. „Înlocuirea sistemelor de comandă şi a tehnologiei de angrenare poate însemna diferenţa în privinţa jurnalizării duratelor, eficienţa energetică sau întreţinerea predictivă,” a concluzionat Stenico.